There should be mass balance across a refinery – every molecule of feed stock that comes in comes back out again (eventually) – and we hope, mostly as useful products. But the reality is that when inputs and outputs are compared there will be some discrepancy. Where does the missing stuff go? Some would have been burnt as fuel, converted into energy and green-house gasses. Some will have been deposited on the catalysts. Some of it definitely gets left behind as a sticky mess at the bottom of the tanks. (I have seen this first hand – and ruined a pair of work boots -- in one of my few contacts with actual rather than digital hydrocarbons when I was given a tour of a refinery in turn-around and we took a walk in a tank emptied for cleaning.) Probably, despite best efforts at containment, some has escaped off into the air – giving the local environs that recognizable “there’s a refinery here” smell.
Wherever it has gone, we probably need to take some account of this in our planning models or they won't be very good at matching actual production. GRTMPS gives you several places to indicate that losses are expected.
Loss in Blending
A loss factor can be entered in the blending area by product by location. [Tables 500.3 and 600.3].
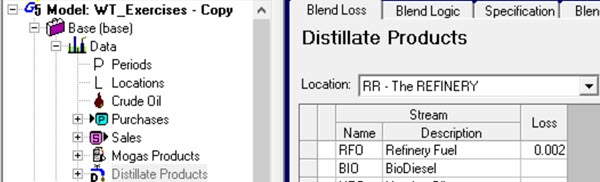
This is the fraction of the component in that doesn’t come out in the final blend.
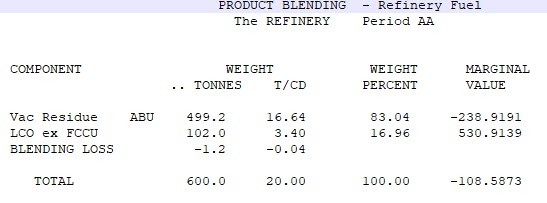
Note that loss factors can’t be entered for pools as they would make it difficult to handle the quality error terms.
Loss in Transportation
Loss factors for transport can also be provided
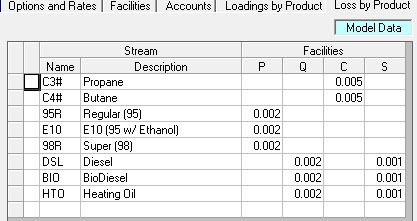
These are given for a particular stream moved by a certain facility. Recently (v5.6 Beta 0.1) a TRANLOSS column was added to TABLE 801.0 so that different factors could be entered for specific movements of a stream from a source to a destination, instead of assuming that all movements on the same facility type had the same loss regardless of locations. This isn’t supported by the database panel yet.
Loss factors for transport can also be provided
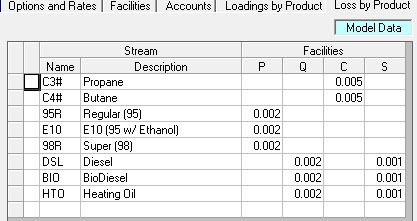
These are given for a particular stream moved by a certain facility. Recently (v5.6 Beta 0.1) a TRANLOSS column was added to TABLE 801.0 so that different factors could be entered for specific movements of a stream from a source to a destination, instead of assuming that all movements on the same facility type had the same loss regardless of locations. This isn’t supported by the database panel yet.
The loss is taken as the material leaves the origin. You can see in the Solution Block Diagram below that more Bio Diesel leaves the refinery than arrives at the terminal.
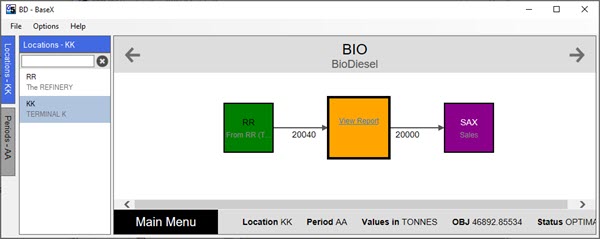
Loss on Process Units
Finally, you can enter loss factors on process units. There is a special row for them in the control section. A value here corresponds to an entry on the special code *LSS in the unit yield table, 2xx.2.
Finally, you can enter loss factors on process units. There is a special row for them in the control section. A value here corresponds to an entry on the special code *LSS in the unit yield table, 2xx.2.
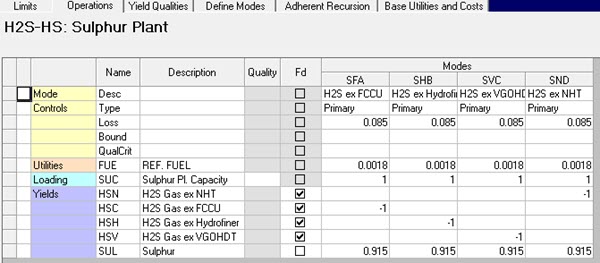
91.5% of the H2S comes out as Sulphur, which is sold. The rest is converted into some waste gasses that are not tracked as a stream. The mass balance is closed by entering a factor in the Loss row so that the vector nets to 0. Without it the DataCheck tool would warn you that the operation is not balanced. This number does not go in the matrix and so has no effect on the optimization. It does, however, have an impact on the reporting. If it is there, the net stream balance will be listed as Expected Loss:
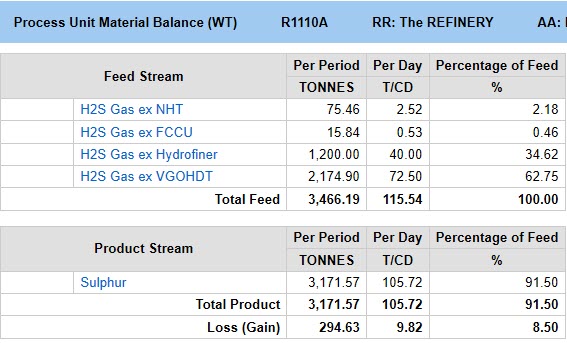
If it is missing, any imbalance will be shown as Unexpected Loss
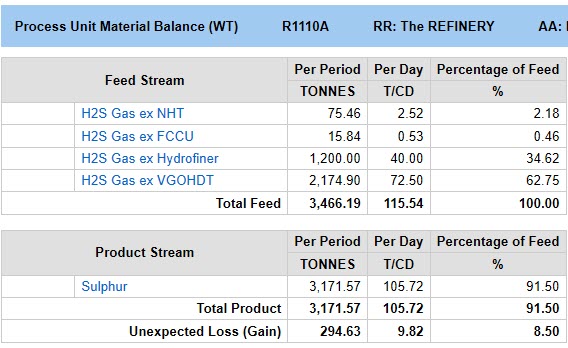
You may see a mix of unexpected and expected values on a unit, if there is a LOSS entry, but it does not close the balance, or if it is given for some operations and not others – even if the unit itself is balanced overall. The expected / unexpected classification is more reliable for the model basis values. I have always thought it was a bit unfair to be told there is an unexpected volume loss or gain when the unit is in mass balance, so from version 5.6 Beta 1.1 if the unit is in mass balance, all volume differences will be labelled expected. In weight models the volume imbalances will be classified in proportion to the weight ones - so if all the mass loss is expected, the volume will be as well.
The hope is that the entered loss value used in the process unit is in some way related to the observed operation – but, of course, it can be just the modeller closing the balance if the values given for the streams don’t add up. This is particularly true in volume balanced models, where the vectors may well not net to zero as there is volume expansion over some units, and volume loss over others. The factor might just be something to tidy up the reporting. A well set up volume model will have the density factors needed to calculate a mass balance, which should, show no unexpected gain or loss. This can be tricky when using traditional static delta-base modelling. If you make use of the non-linear modelling features, there is no excuse for being out of balance in a converged solution, however, as you can keep the densities in line with the net predicted yields.
Overall Loss
The total loss over a location or location group is shown in the Input/Output reports.
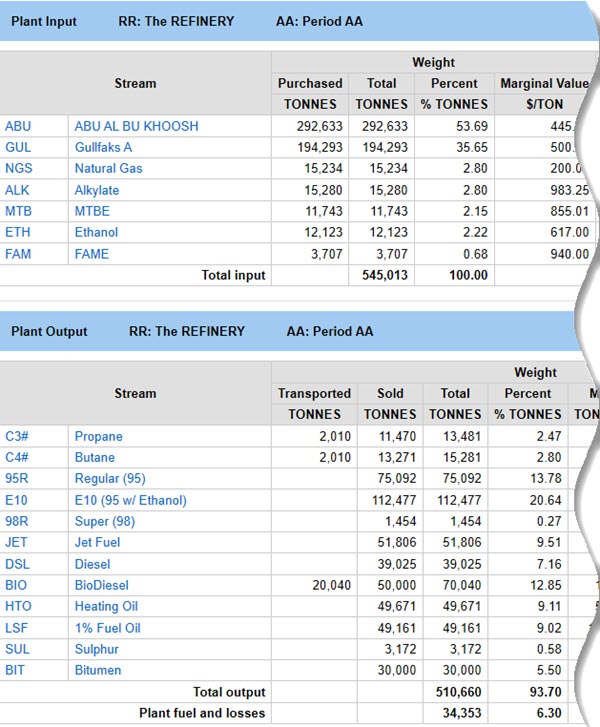
The numbers in the Plant Fuel and Losses row are simply calculated from the different between the total tonnes in and out - not by adding up all the reported LOSS from the factors used on the activities – so there is no distinction here between expected and unexpected.
Internal Consumptions
The missing mass is labelled “Plant Fuel and Losses”, because the internal consumptions – fuel oil or gas – that are burnt to generate the energy for the processing will be part of the net difference. They are normally as modelled as converting to utility and loss, like so, from the WT demo model:
The missing mass is labelled “Plant Fuel and Losses”, because the internal consumptions – fuel oil or gas – that are burnt to generate the energy for the processing will be part of the net difference. They are normally as modelled as converting to utility and loss, like so, from the WT demo model:
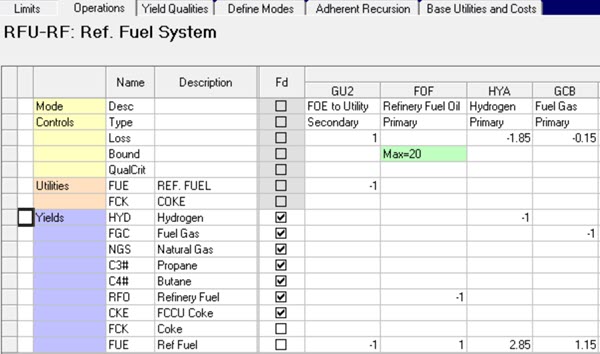
All the different fuels – the picture shows a sub-set -- are converted to a single stream “FUE”. The rate of conversion corresponds to the energy content – so it takes more fuel gas and even more hydrogen to be equivalent to a single ton of refinery fuel oil. On the GU2 operation, that collected Fuel equivalent material is converted to FUE utility. (The negative number in the utility row indicates a production, while the processes that consume the energy will have a positive value – the reverse of the stream balances.). The value in LOSS row makes each vector net out to zero.
You can get a break down of the material used as process fuel like so:
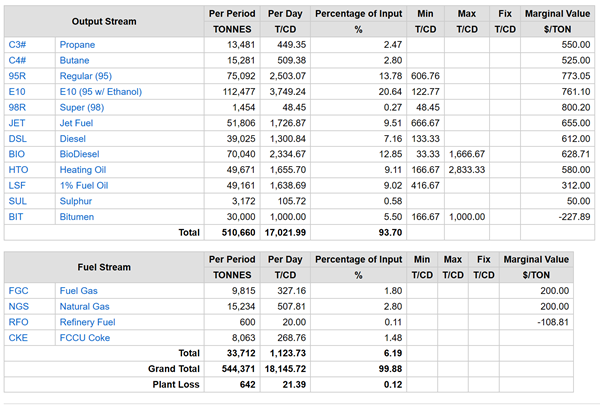
This is triggered by marking the unit(s) that consume them as “Fuel” in the Process Unit list (TABLE 200.0, $FUEL).
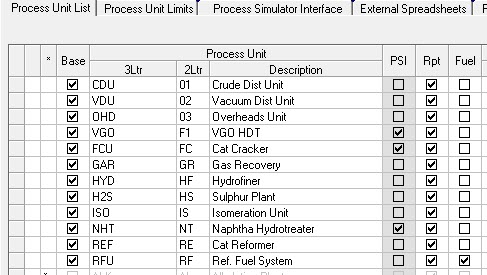
Loss Modelling in Practice
Almost every model I have seen with process units in it, has LOSS factors set. Without knowing the thinking behind, it is not possible to say if these represent a tuning of the model to observed balance, or are simply there to keep things tidy. Some modellers prefer to define loss streams explicitly; these are produced on the units and sold at a zero price. Then the overall balance report, would show the loss stream in the outputs and any remaining net difference would be the unexplained. You could also have multiple streams if you wanted to differentiate losses from sub-sections of the plant.
Almost every model I have seen with process units in it, has LOSS factors set. Without knowing the thinking behind, it is not possible to say if these represent a tuning of the model to observed balance, or are simply there to keep things tidy. Some modellers prefer to define loss streams explicitly; these are produced on the units and sold at a zero price. Then the overall balance report, would show the loss stream in the outputs and any remaining net difference would be the unexplained. You could also have multiple streams if you wanted to differentiate losses from sub-sections of the plant.
There are some models where the overall loss is taken off right at the beginning. In the model of the main distillation towers something like 1.05 tons of feed comes out as 1 ton of product. This is a convenient way of taking into account a typical observed loss without assigning it to a specific activity. A few models use the blend factors as well, but these are not common. Models with transportation options sometimes use the loss factors – sometimes not.
My impression is that over the last few decades there has been a trend to expect better actual accounting of physical volumes, and less loss from activities. So models are less likely to have factors for losses except where there are known conversions to waste material or modelling place holders. However, it is quite likely that there will still be some other disappearances. Should you take your typical observed loss out of the model, so the targets include the expectation that it will occur? Do you set the targets to an idealised level, with the expectation that this can and should be minimized during operations, using a scheduling system and advanced control procedures? Your decision.
From Kathy's Desk
24th January 2020 and updated 25th February 2020.
24th January 2020 and updated 25th February 2020.
Comments and suggestions gratefully received via the usual e-mail addresses or here.
You may also use this form to ask to be added to the distribution list so that you are notified via e-mail when new articles are posted.
You may also use this form to ask to be added to the distribution list so that you are notified via e-mail when new articles are posted.